Table of Contents
I will share six aspects you need to consider while choosing an aerosol propellant.
In this article, you will learn about:
- What is the vapor pressure of the different propellant gases?
- What is the effect of the solubility of different propellants on the sprayeffect?
- What is the ratio of each propellant used in the product?
1. Vapor Pressure

You decide which propellant gas to use for the application of the product.
In addition, for a large portion of the products, you decide which propellant gas touse based on the desired spray properties to be formed.
The propellant gas has a certain vapor pressure so that when the valve is pressed,it can carry the material quickly and evenly ejected.
This is the primary performance that the propellant should have.
The higher the propellant pressure is, the faster the spraying will be, and the morethoroughly the material is sprayed.
But limited to the pressure container (aerosol cans) pressure resistance capacity,the propellant pressure can not be too high.
In addition, seasonal temperature changes can affect the propellant pressure.
You need to ensure that the propellant gas still has a certain vapor pressure at lowtemperatures to propel the material out.
And at high temperatures, the vapor pressure should not be too high not to exceedthe aerosol can’s safety pressure.
Therefore, the appropriate temperature vapor pressure curve is an essentialindicator for evaluating propellants.
To meet this need, you can achieve such a propellant by compounding, such as F11/F12, propane/butane, etc.
The following figure shows the temperature vapor pressure profile of some propellants.
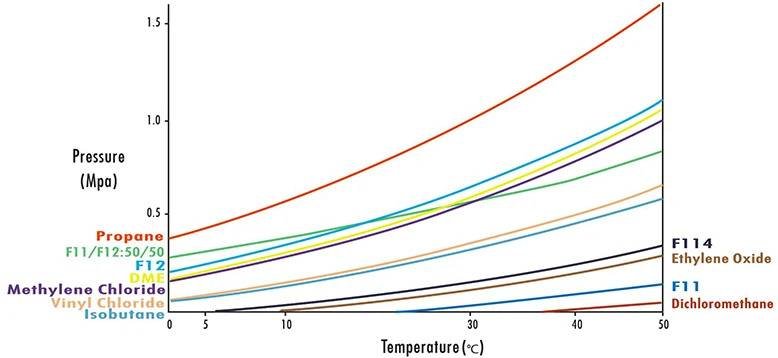
2. Solubility
In addition to acting as a throwing agent, the propellant is often used as a solventand a diluting agent for the material in the aerosol.The more the propellant is dissolved into the material, the more even and fine thespray is.
Therefore, solubility is also an essential factor.
The below table displays the dissolution properties of each type of propellant.
Since most propellants are poorly inter-soluble, many factories dissolve thematerial in a solvent that is inter-soluble with the propellant, and then fill it into the can.
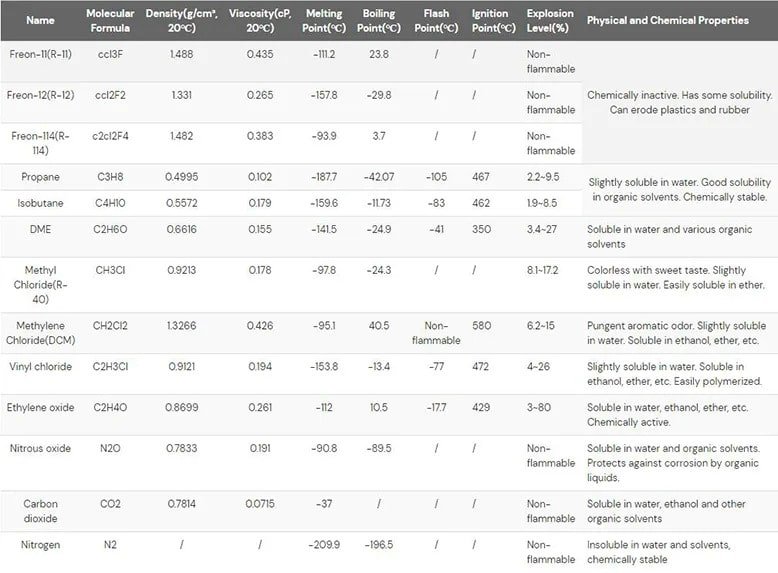
3. Safety
Most solvents of the materials are flammable and volatile liquids such as ethanol, isopropyl alcohol, deodorant kerosene, etc.
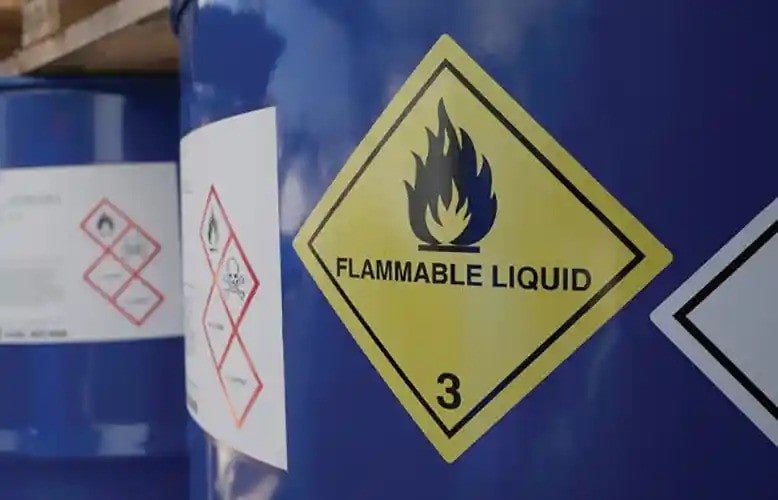
And most products are used at home or in public places.
Therefore, you need to make sure that the flammability and explosiveness of the products are low to ensure the use safety.
However, most propellants are flammable and explosive.
And Freon, which has a better safety profile, has been gradually banned for environmental reasons.
Inert gases such as carbon dioxide and nitrogen are used less frequently because they are too insoluble and cannot be liquefied.
4. Toxicity

Most aerosol products are used at home.
Many products come into direct contact with the human body, such as cosmetics, pharmaceuticals, food, etc.
Therefore, you should have high requirements for the toxicity control of propellants.
It would be best if you chose different propellants according to different products.
The table below lists some propellants’ toxicity levels, the entry route, the degree of harm to humans, etc.
5. Environmental Pollution

The aerosol product is sprayed and dispersed over the air and object surface.
On the other hand, propellants quickly evaporate into the air and have a certain impact on the environment.
Therefore, propellants’ degree of environmental pollution is also an essential factor in selecting propellants.
6. Price

The price of the propellant is another crucial factor in the selection.
The highest Freon is about more than CNY 10,000 per ton(may differ in your area).
Propane, butane, and Dimethyl Ether are priced between CNY 4,000 and 5,000(may differ in your area).
Compressed gas has the lowest price.
The remaining special propellants are used in specific products, and the price factor is less considered.
Comparison of Various Propellants' Applications
Below I will share the application of common propellants in aerosol products.
Each type has its own characteristics.
Some have been abandoned as society evolves.
See if there is one below that you are using.
Freon
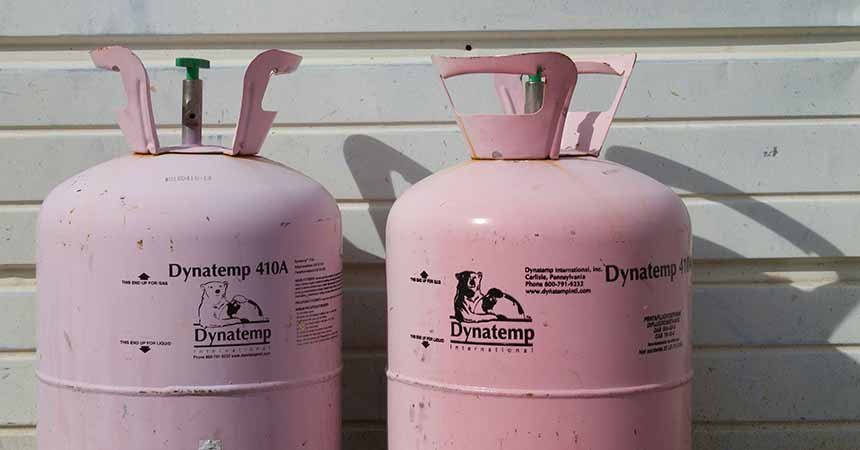
Freon was widely used in aerosol products in 1950~1970 because it is non-toxic and safe.
And factories can compound several kinds of Freon in different proportions.
The compounded propellant can meet the requirement of the temperature vapor pressure curve of propellant for various aerosol products.
In 1978, the U.S. Environmental Protection Agency (EPA) banned Freon as a propellant for aerosol products.
Countries around the world have subsequently phased out Freon as an aerosol propellant.
Butane/Propane(LPG)
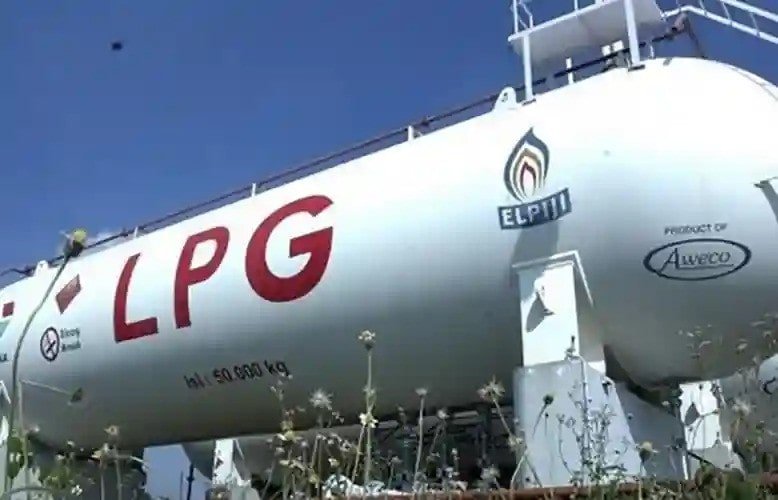
We can adjust the ratio of propane and butane to change the LPG vapor pressure.
So that its temperature vapor pressure curve can be better than that of Freon. (seeTemperature Vapor Pressure Curve above)
In this way, we can meet the vapor pressure requirements of various aerosol products and also meet the requirements of aerosol products for spray properties.
The chemical properties of LPG are relatively stable.
It does not react with acids and alkali and is not easily hydrolyzed.
Therefore, LPG is suitable for cosmetic aerosol products such as shaving cream and pharmaceuticals.
Moreover, it is also widely used in insecticide aerosol due to its wetting property to insect wings.
At the same time, its low viscosity helps atomization and can produce small droplets suspended in the air for a long time.
In producing emulsion products, it has the function of secondary foaming, and the foam stays longer.
Propane/butane is miscible with most organic solvents.
However, it has poor solubility with water.
This drawback limits the scope of application to some extent.
We can solve it by using special specification valves and shaking before use (such as mousse).
In traditional aerosol products, propane/butane propellant use has accounted for more than 90%, and compressed gas accounted for 5%, the other 4%.
Dimethyl Ether(DME)
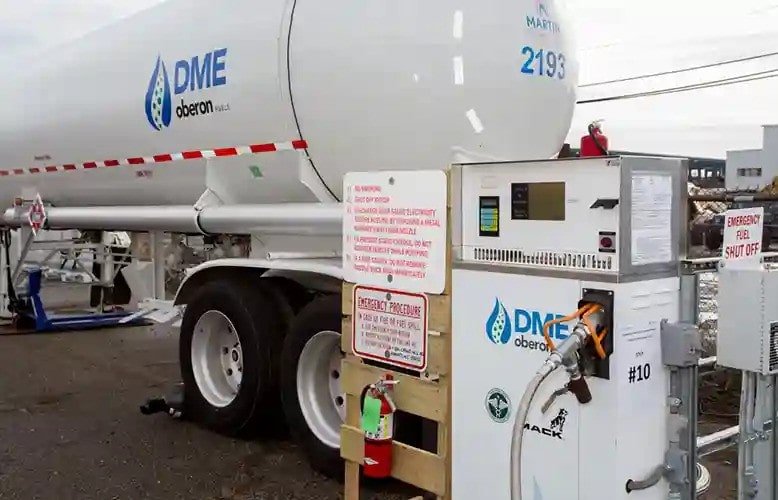
Dimethyl ether(DME) is colorless, odorless, and has low surface tension and viscosity.
DME has good mutual solubility with water and most organic solvents.
Dimethyl ether is chemically stable, and its safety is good after compounding with water.
However, the vapor pressure is steeper and higher at high temperatures (see the figure below), making it more dangerous during storage and transportation.
Fluorine/Chlorine Hydrocarbon
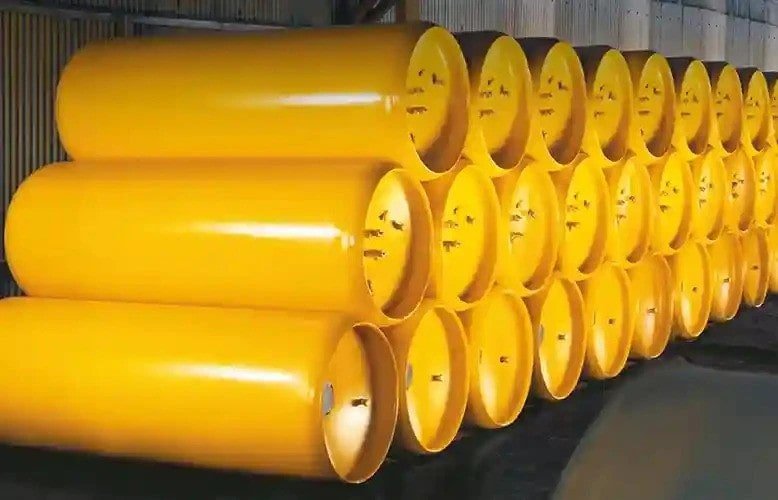
It includes octafluorocyclobutane, vinyl chloride, chloromethane, dichloromethane, etc.
Although these propellants also have fluorine and chlorine atoms, they do not damage the ozone layer.
They are generally non-flammable and have better safety and solubility than LPG.
Because it contains fluorine or chlorine atoms to pollute the environment and is more toxic, it is not widely used.
Compressed Gases
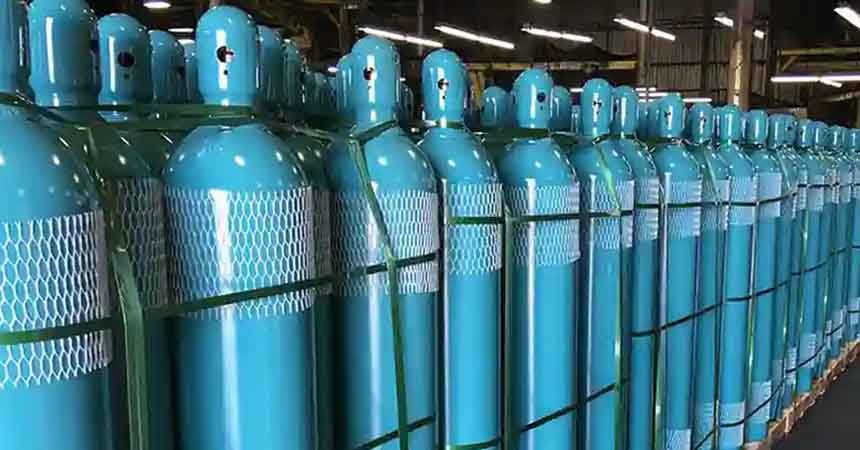
These gases include ammonia, carbon dioxide, nitrous oxide, etc.
Their most significant advantage is their safety, non-pollution, and low price.
However, they are insoluble in liquid and have high pressure in the can.
In the process of use, as the amount of liquid decreases, the amount of each spraying also decreases, resulting in incomplete product delivery.
At the same time, the droplet size is large.
And there is a possibility of leakage of the propellant when the can is placed upside down.
All these drawbacks limit its wide use.
Conclusion
This is so much for today’s article on aspects for propellant choosing.
Then, my question is:
- What products are you looking to do?
- What propellant are you considering?